Case study: Norsk Gjenvinning’s waste wood shredding line in Norway
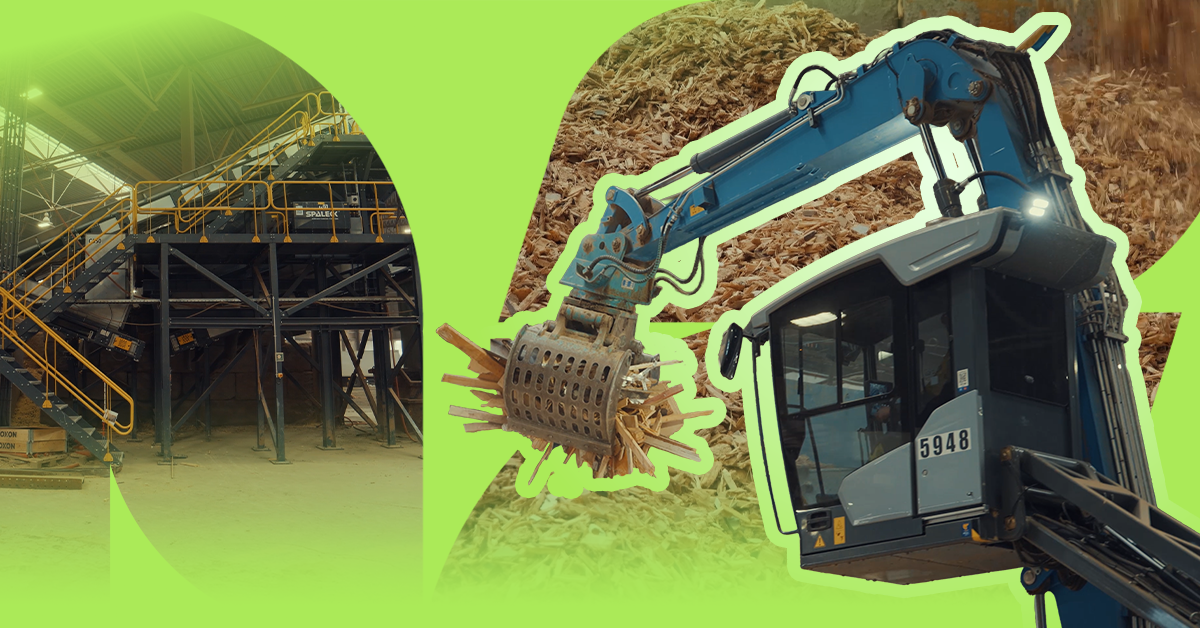
RECAP
- Built in 2022 as a modern wood shredding line in Oslo, it is capable of processing up to 35 t/hour depending on material composition and 90,000 t/yearly.
- Produces high-quality wood chips that meet the ISO P63 standard, making them suitable for both energy production and furniture manufacturing.
- Installation on site was fully completed in just 3 weeks and with no actual downtime thanks to a temporary production line.
TOWARD A CIRCULAR FUTURE
NG Group (Norsk Gjenvinning) is the leading environmental services provider in the Nordic region, operating at the forefront of circular economy solutions. The company manages over two million tonnes of waste annually and transforms it into valuable secondary raw materials for a wide range of industries. With a strong commitment to innovation and sustainability, NG Group plays a pivotal role in building a resource-efficient future across the Nordic region.
In 2022, NG Group initiated a major upgrade to its waste wood shredding operations at its Oslo facility. The objective was to replace an aging system with a new high-performance line capable of producing consistent, high-quality output that meets the ISO P63 standard. This upgrade was essential to support growing material demand, improve processing efficiency, and strengthen supply stability to downstream customers.
The project was also designed to be completed next to the existing operational line with minimal disruption to ongoing production.
BALANCING PRECISION, PRODUCTION, AND PERFORMANCE
From the outset, NG Group had a clear set of technical and operational requirements for its new waste wood shredding line. The upgraded system needed to process up to 90,000 tons of waste wood annually and deliver a high-quality output suitable for both energy production and material reuse, particularly in the furniture industry. Achieving the ISO P63 standard for chip size was a non-negotiable requirement, ensuring the final product met strict quality criteria for downstream use.
In addition to output quality, NG emphasized the importance of reducing oversized and fine fractions, both of which diminish material value and recovery efficiency. The system needed to produce a clean, consistent wood chip fraction while minimizing unnecessary shredding and maximizing yield from each ton of input material.
The logistical challenges were equally demanding. The new line had to be installed within an active processing facility, directly adjacent to the existing operational line. This required a carefully phased plan to decommission old equipment, install the new system, and maintain continuous production, all within a tight three-week installation window.
Executing the project under these constraints required precise coordination, adaptive planning, and close collaboration among NG Group, Azortum, and other involved contractors.
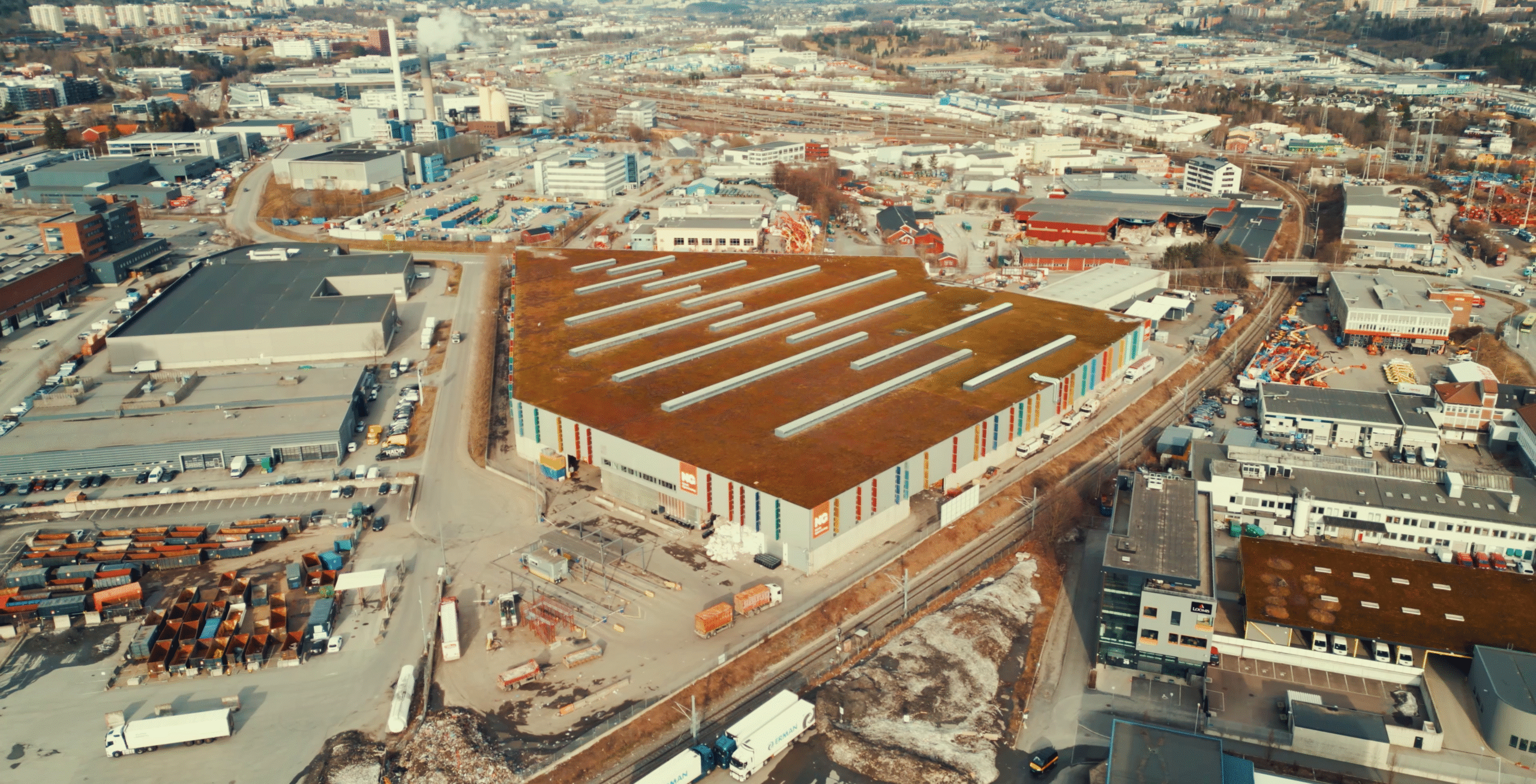
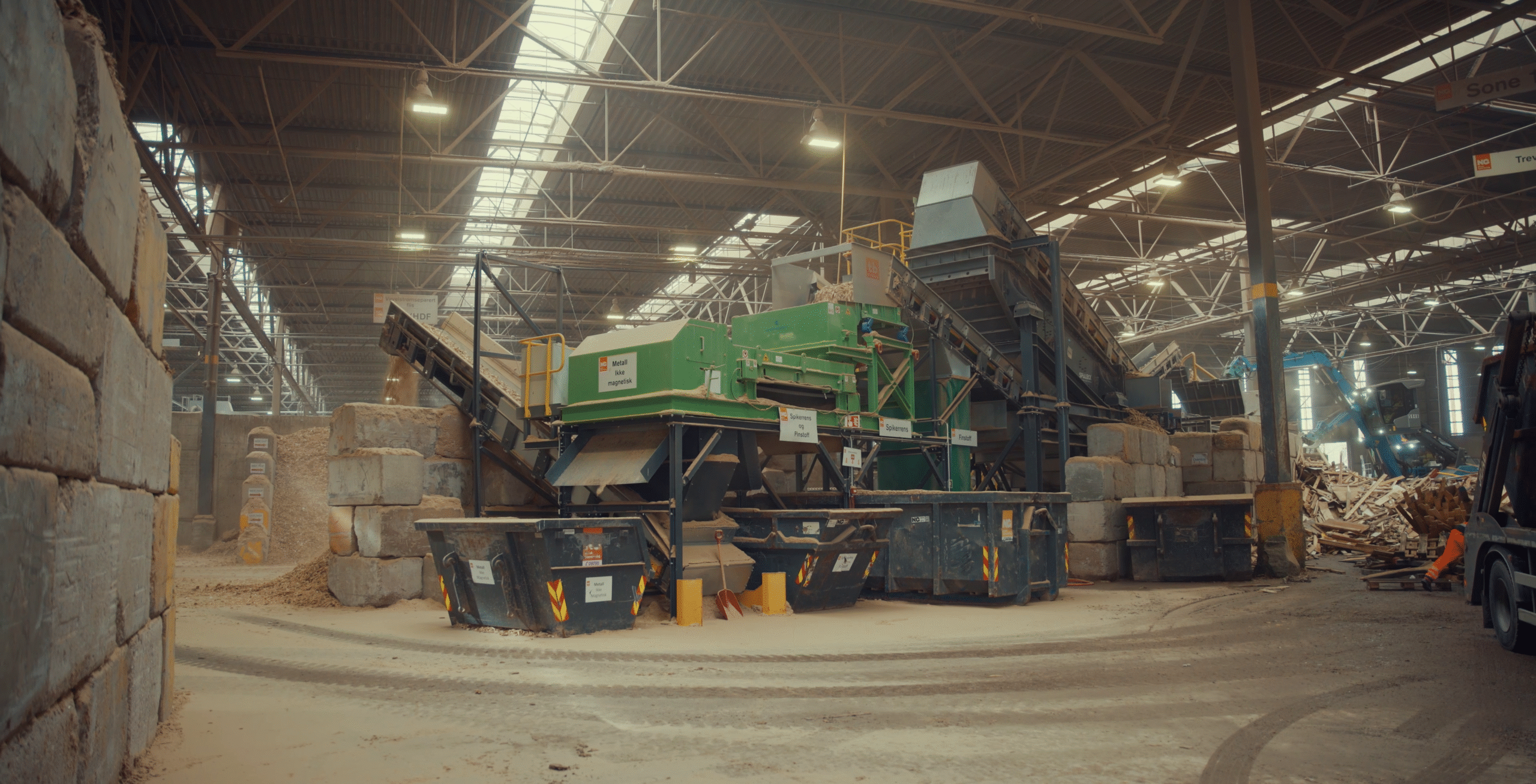
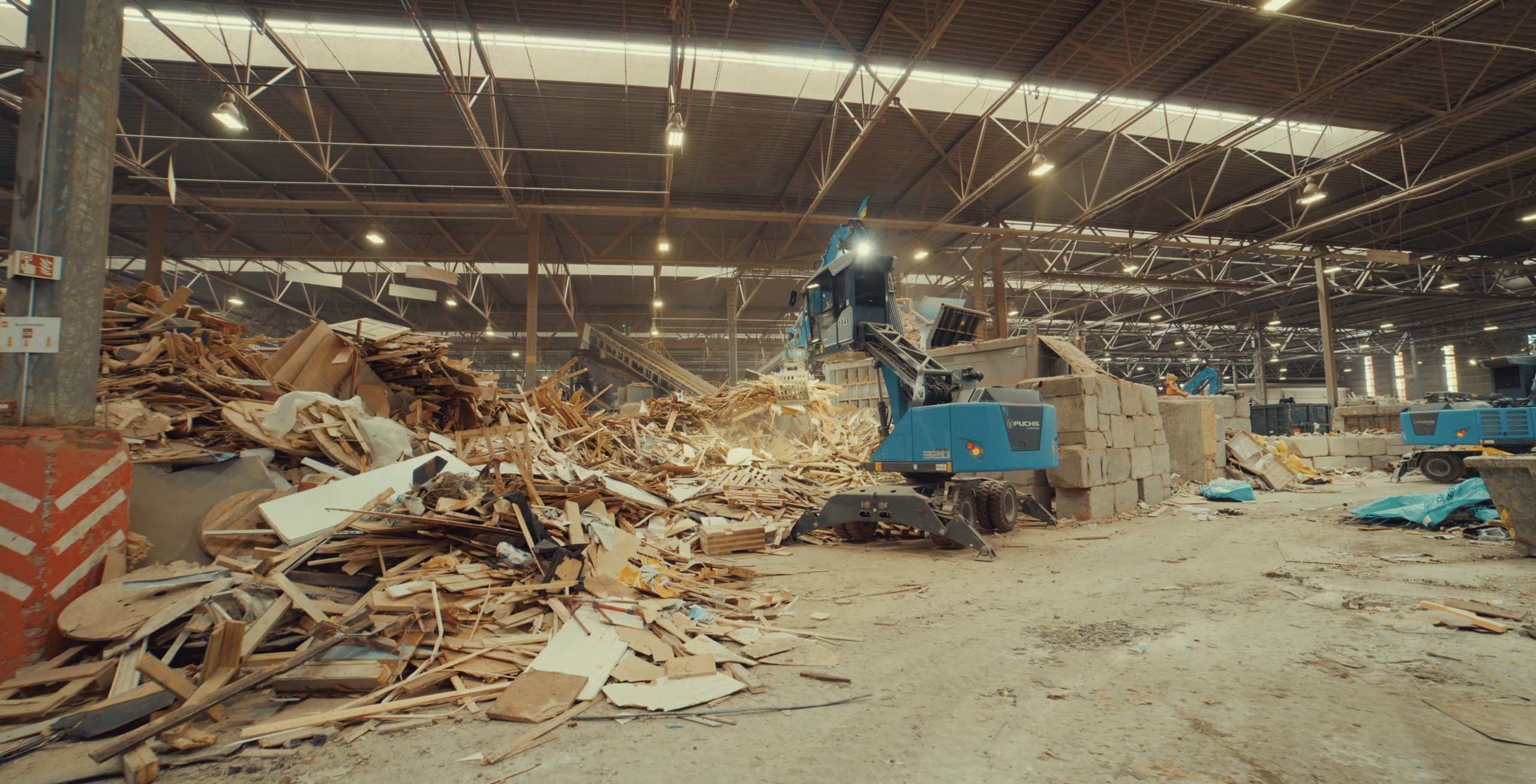
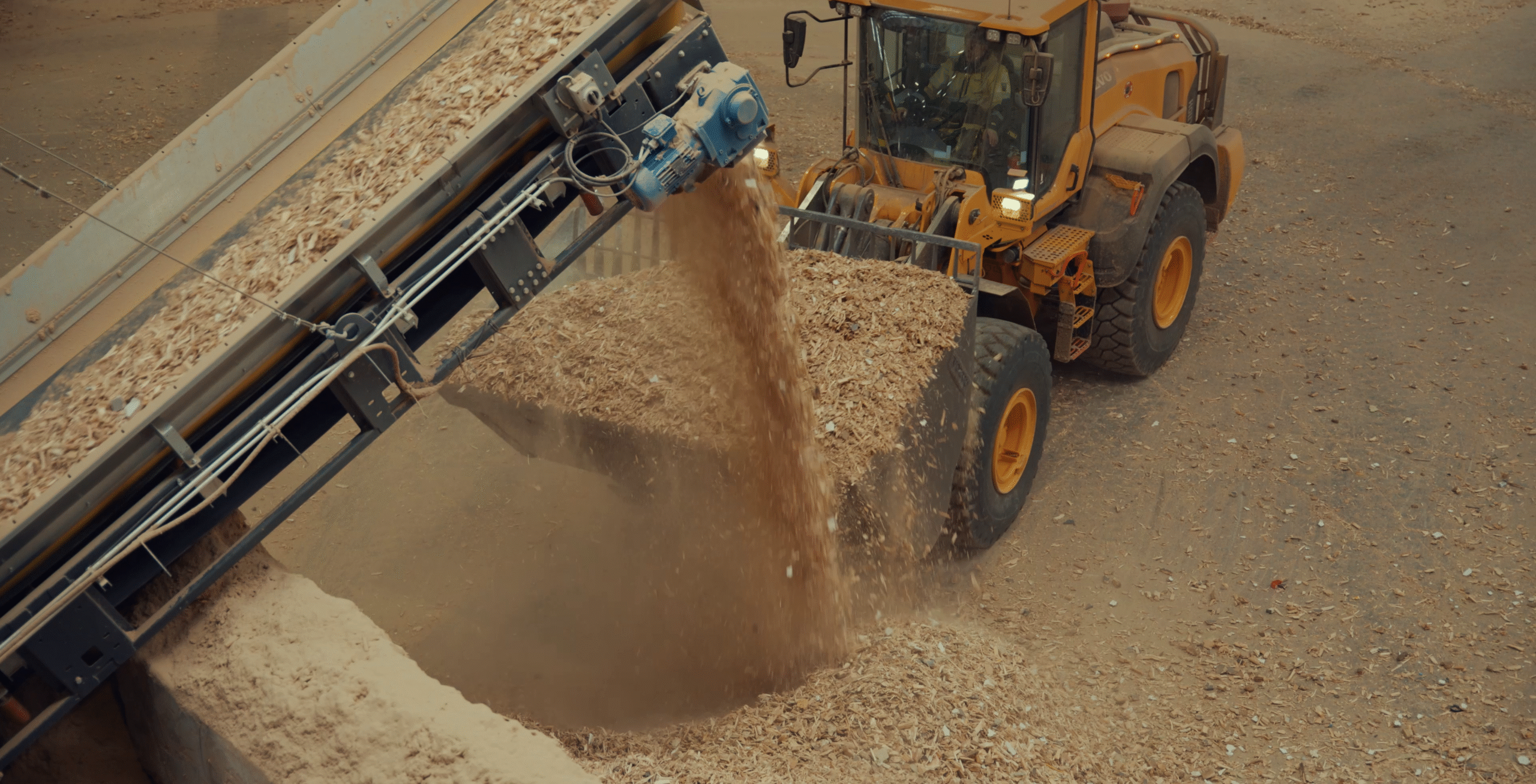
SMART DESIGN FOR SMARTER RESOURCE RECOVERY
To meet NG Group's stringent requirements, Azortum delivered a modern wood shredding line engineered for precision, durability, and adaptability. The design prioritized material quality, operational reliability, and minimal environmental impact, while fitting seamlessly into an existing facility with no room for production delays.
The new line begins with a primary shredder, which reduces incoming wood waste to a preliminary size. From there, material passes through a magnetic separator that extracts ferrous metals, followed by a screening unit that filters the desired fraction and redirects oversized material back to the shredder for reprocessing. The final product is then passed through an eddy current separator, which removes both remaining ferrous and non-ferrous metals, resulting in a clean, market-ready output.
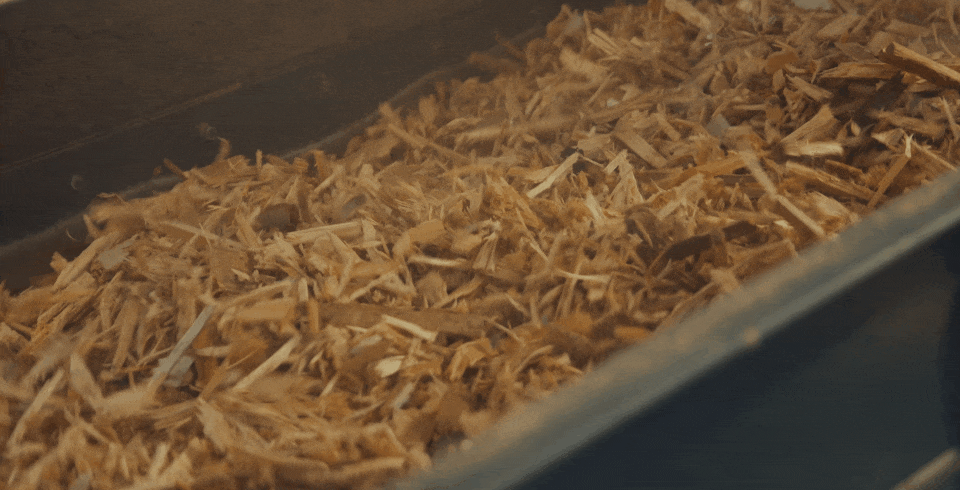
One of the key innovations was the system's ability to minimize fine material, which is a low-value byproduct. This is achieved by controlling the amount of wood that is shredded.
This approach ensures a higher yield of valuable output from the same amount of raw material. The screening unit also allows operators to adjust hole sizes, making it easy to customize the final fraction based on specific recovery needs.
The entire installation was executed with precision. Ultimately, the wood shredding line was installed and operational with no downtime and minimal production loss thanks to a temporary production line on the side. Through tight coordination and phased commissioning, NG Group successfully maintained its waste intake and output throughout the project.
SUPPLYING SOLUTIONS TO NG'S PROBLEMS
Following the successful commissioning of the new shredding line, NG Group expressed strong satisfaction with both the system performance and Azortum's collaboration throughout the project. One of the most valued outcomes has been the predictability and consistency of the end product, which reliably meets the ISO P63 standard across production cycles.
The line's ability to produce high-quality fractions suitable for both energy recovery and material reuse has strengthened NG's position with downstream customers. They highlighted the stability and performance of the system as key enablers of supply chain reliability.
Azortum's post-installation support also received high praise, says Technical Project Manager Peter Sjølie Callister:
- "Azortum has been very responsive when we have reached out to help get support in small issues or corrections of the new production line. And we have the impression that they really want us to be satisfied in the end with the product or the system they have delivered."
With the new shredding line in place, NG Group is better equipped than ever to meet the region's rising demand for high-quality secondary materials, doing it reliably, efficiently, and sustainably.
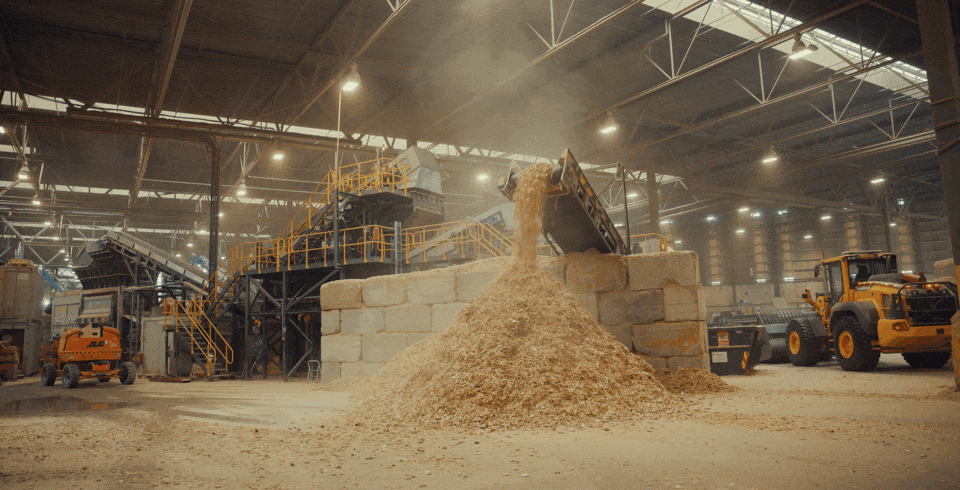
Write us about your project!
At Azortum, we are committed to developing unique solutions that are sustainable to operate and profitable for your company.
We have received your information and will be in touch with you shortly. Thanks!