Case study: Ragn-Sells’ Plastic Packaging Waste and Waste Paper Sorting Line
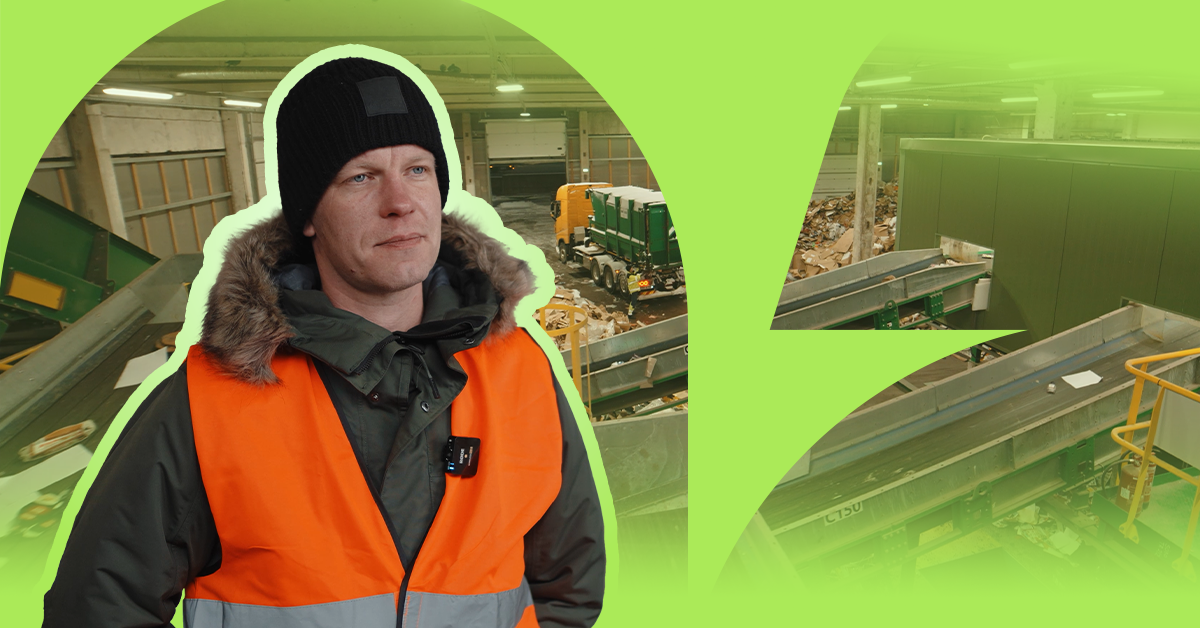
RECAP
- Ragn-Sells is a circular economy company, whose primary process involves the collection and sorting of packaging waste.
- They approached Azortum with the goal of improving their paper sorting line and increasing it’s throughput more than two times. Additionally, Ragn-Sells also wanted to add packaging sorting into the same line.
- As a result, the new line improved the capacity from 3 tons an hour to 6 tons per hour, while at the same time reducing the residue rate.
THE REASONING BEHIND IMPROVING THE LINE
Ragn-Sells has adopted a fresh perspective on waste. Their focus is on building a more circular economy, where raw materials are extracted directly from waste. In this way, waste will be utilized with maximum efficiency.
In Estonia, they handle a significant amount of MSW waste, while the remaining bulk waste includes construction waste, C&I waste and other sources of raw materials.
Our history with Ragn-Sells Estonia goes back to 2011 when we first helped them build their fully automatic municipal solid waste (MSW) sorting plant. In 2019, we helped Ragn-Sells build their hazardous waste sorting shredding.
One of our main collaborations has been at the mixed paper and packaging sorting plant in Tallinn, where Azortum helped Ragn-Sells expand and improve its operating line.
Here, Ragn-Sells manages the collection, sorting and transportation of waste paper and plastic packaging. Sorted materials are then forwarded to end recyclers and companies that use them to produce new products.
As Sven Ruukholm, Head of Ragn-Sells Estonia’s Treatment and Detox put it:
- “We chose Azortum for this project because we have had a very good relationship in the past with different projects.”
The main reason behind improving the old line was its capacity. Material was put into the line one way and people had to manually do the positive sorting to take out the needed materials.
The goal was to improve the throughput by introducing machines, that do most of the heavy lifting. This upgrade would reduce the crew size working on the line and they could be allocated from material sorting to quality control.
Another goal of the project was to add a mixed packaging waste sorting solution to the existing line.
Because OCC and paper collection were on the rise and the tons were rapidly increasing, we decided to meet these goals in different phases. We first decided to improve the existing mixed paper OCC sorting line in 2020 and planned the expansion of the packaging sorting line for 2022.
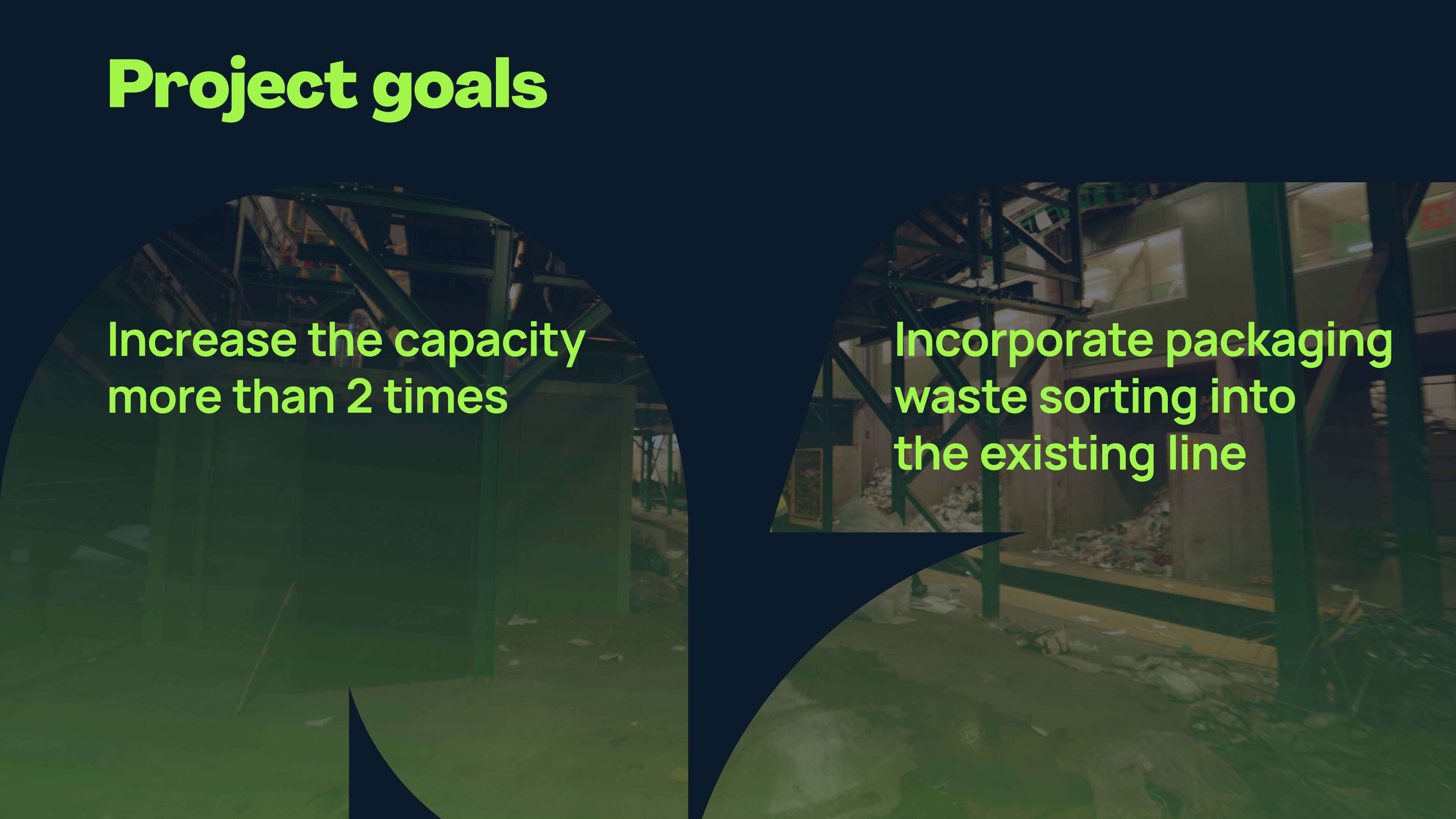
CHALLENGES AND SOLUTIONS
Both paper and plastic material flows require a flexible system to handle them. To reach the two main goals, we first had to overcome challenges.
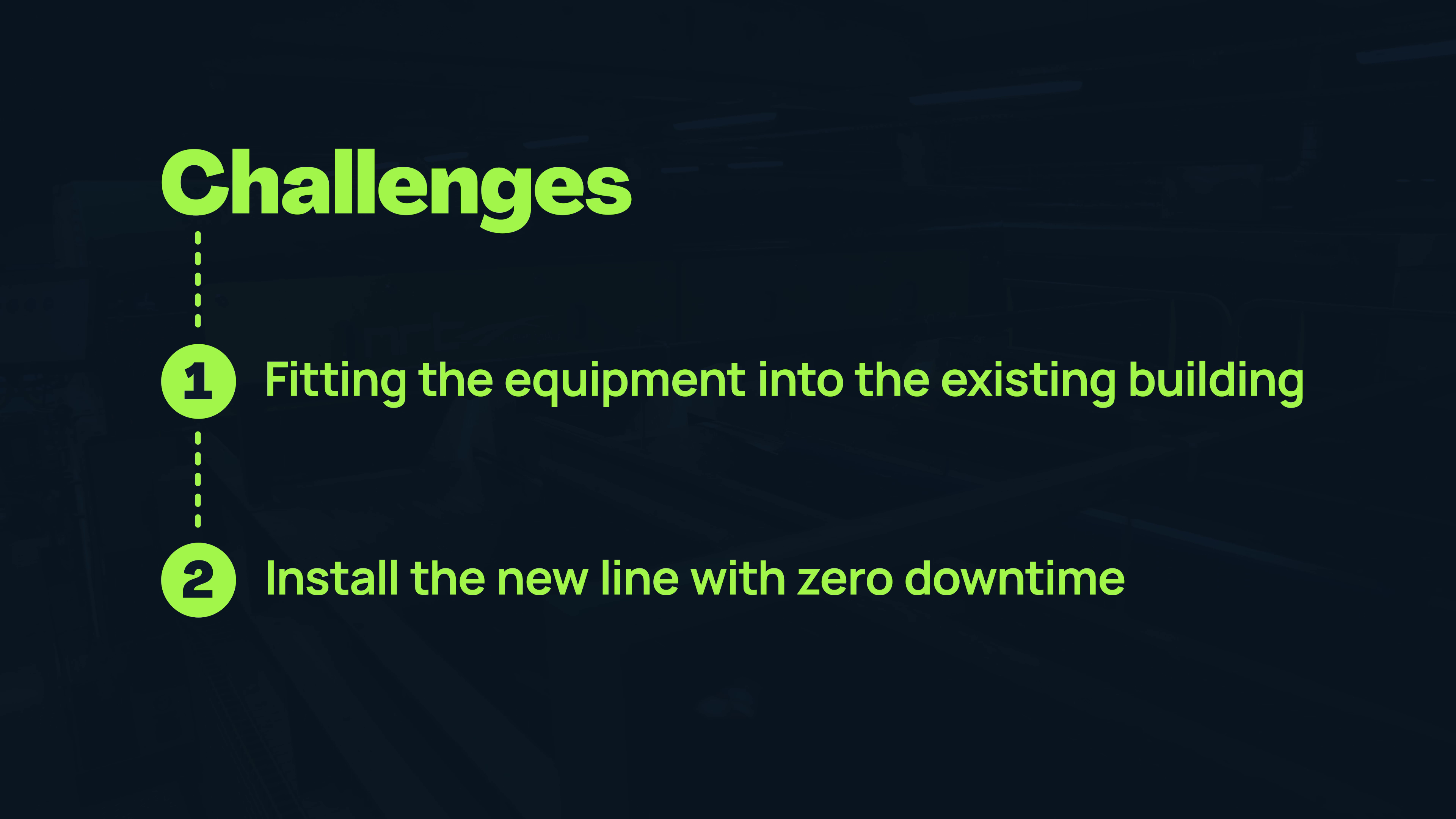
RESULTS AND IMPACT
The new improved line yielded significant outcomes.
The existing throughput was enhanced greatly. The previous capacity of the line doubled from 3 tons an hour to 6, which significantly boosted the operational efficiency of the plant.
Residue rates also fell, as new sorting technologies were implemented to the line. This led to a notable decrease, that helped maximize material recovery and get more material out from the flows.
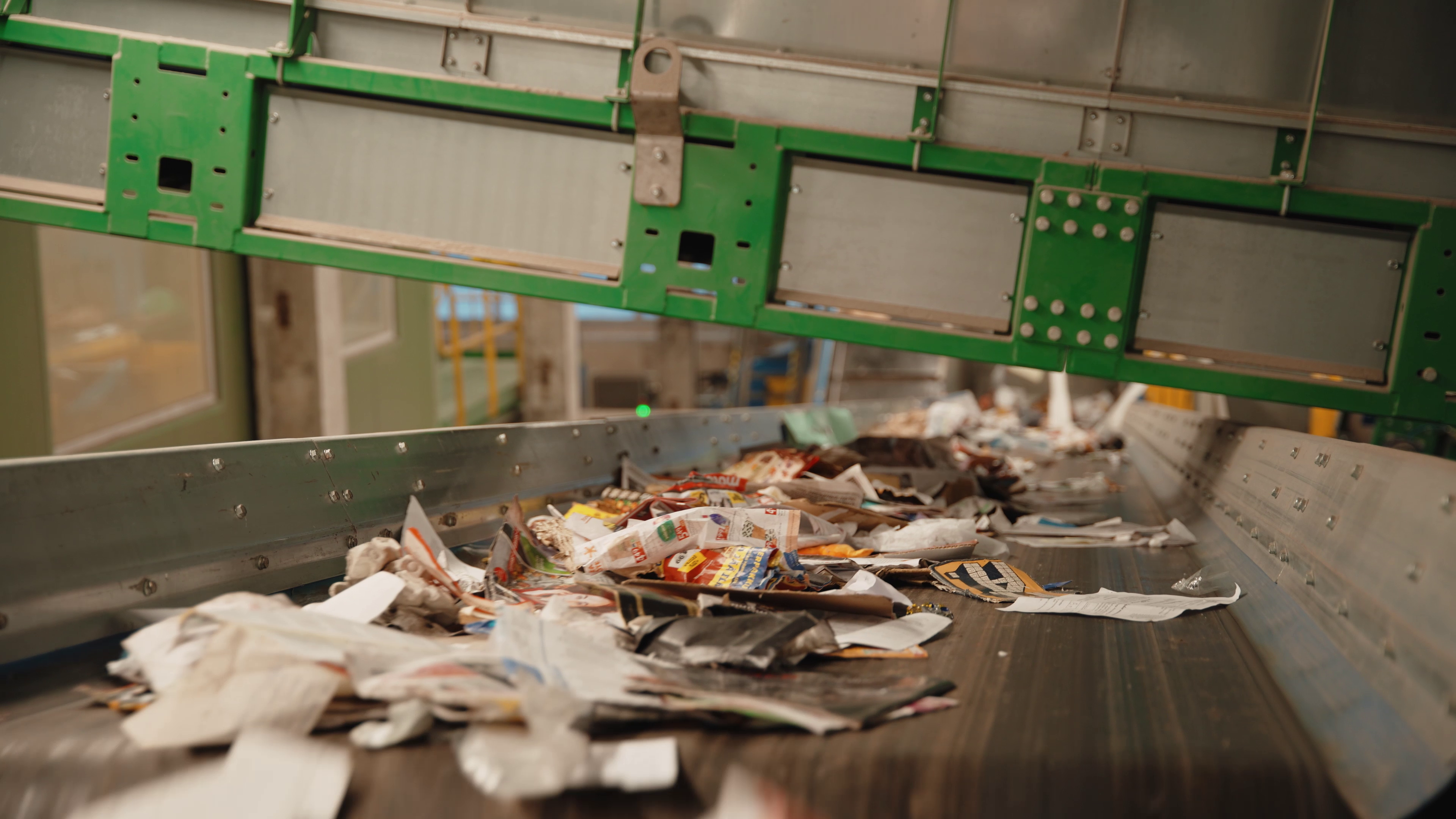
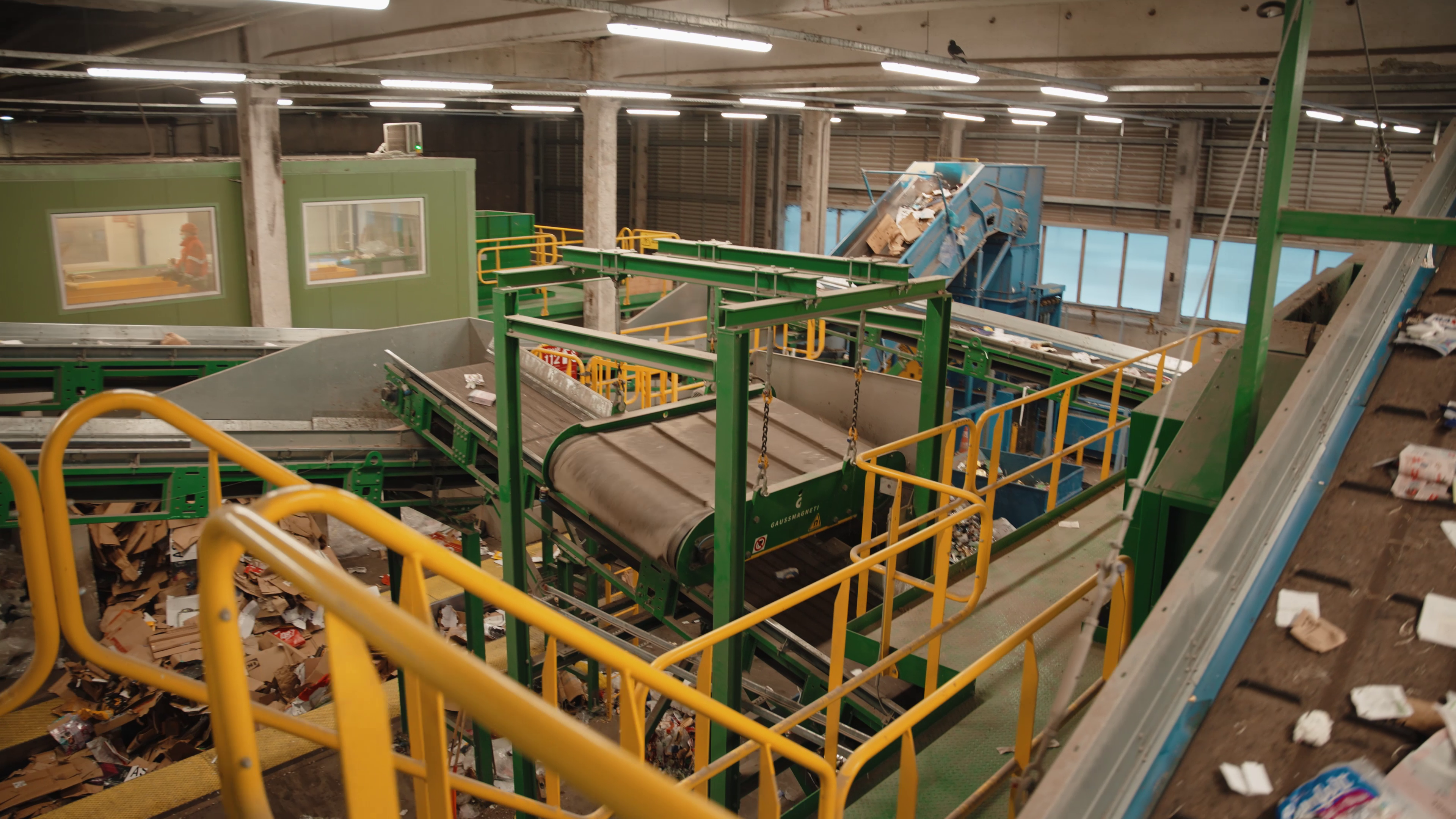
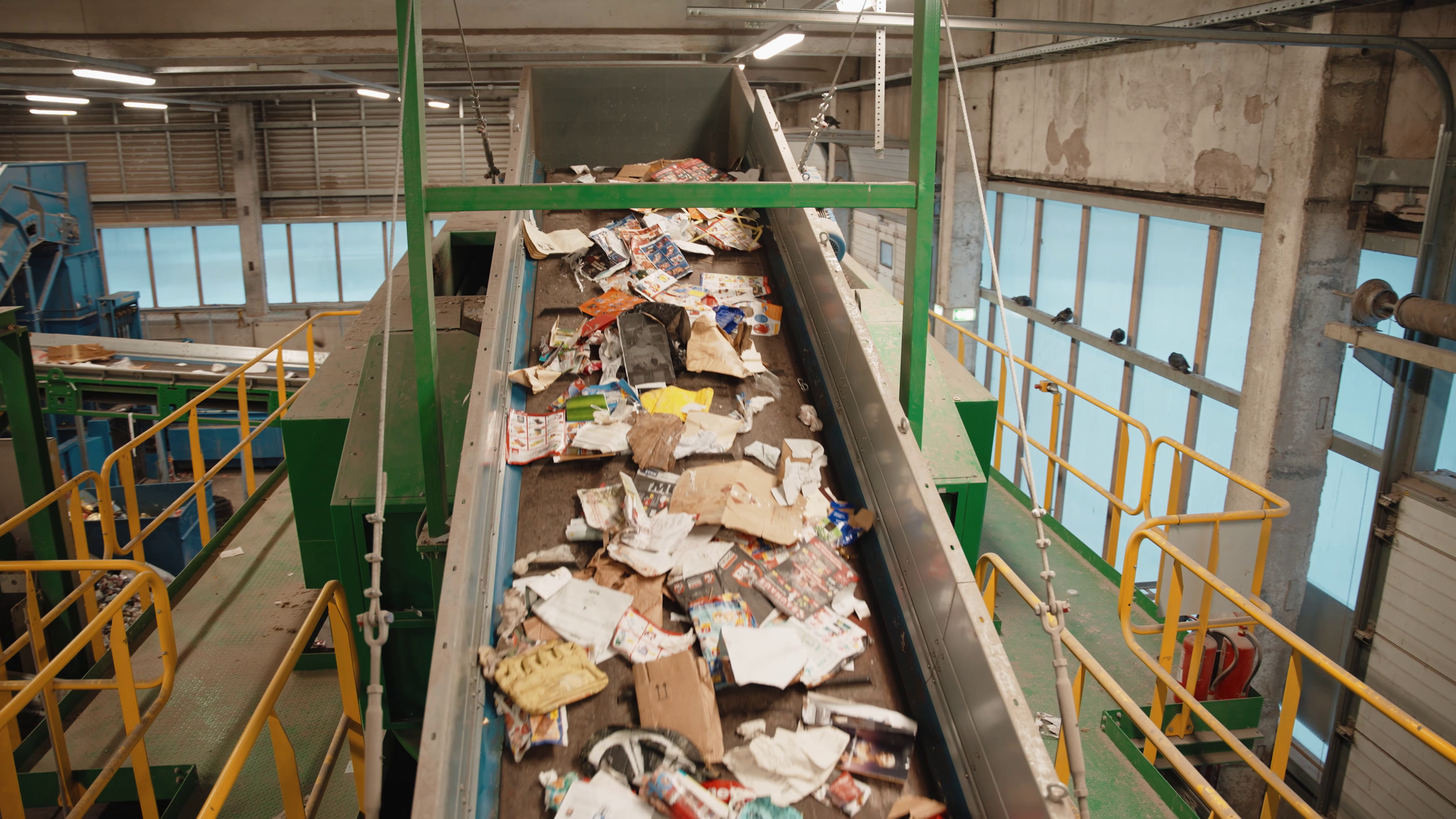
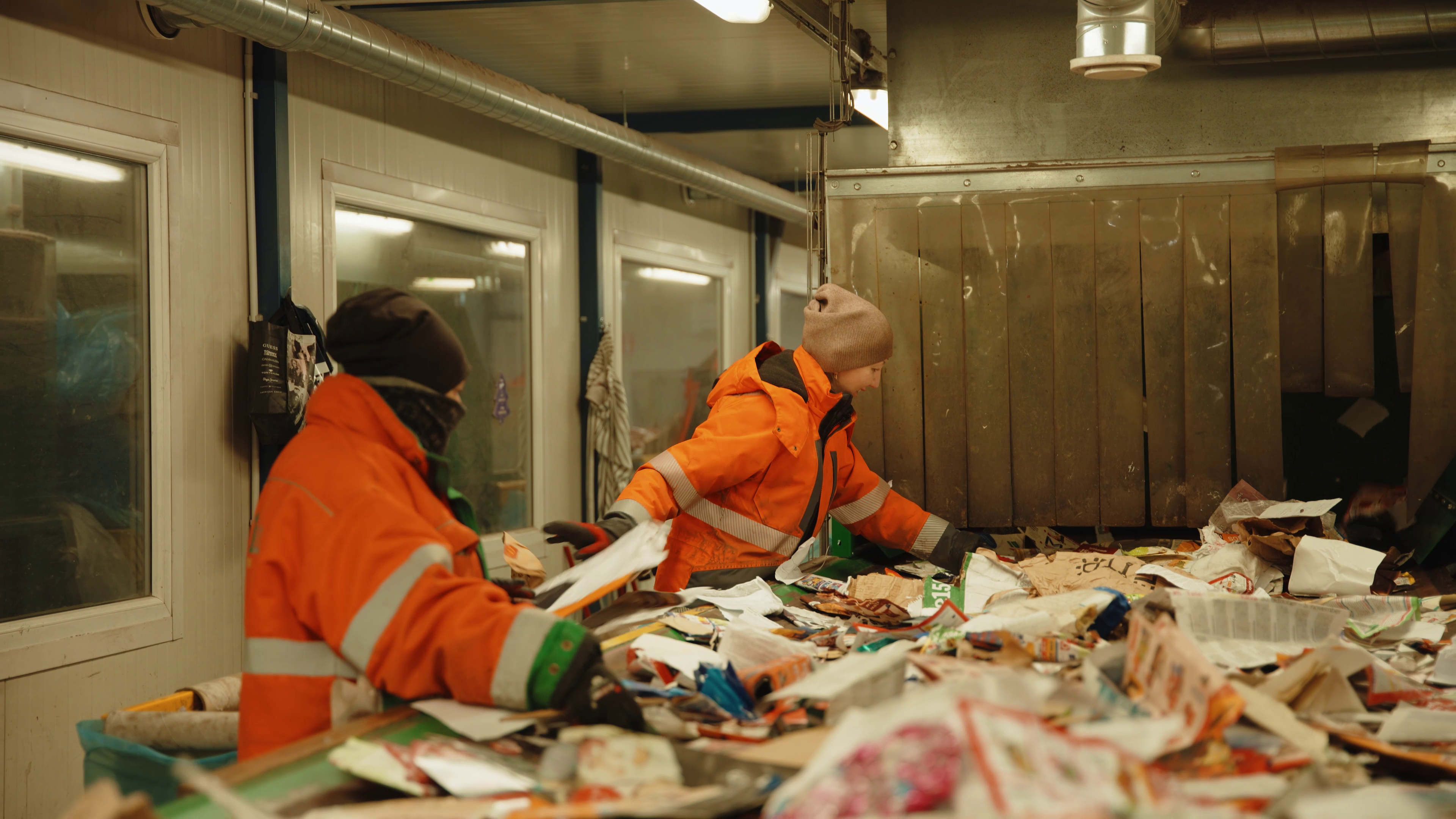
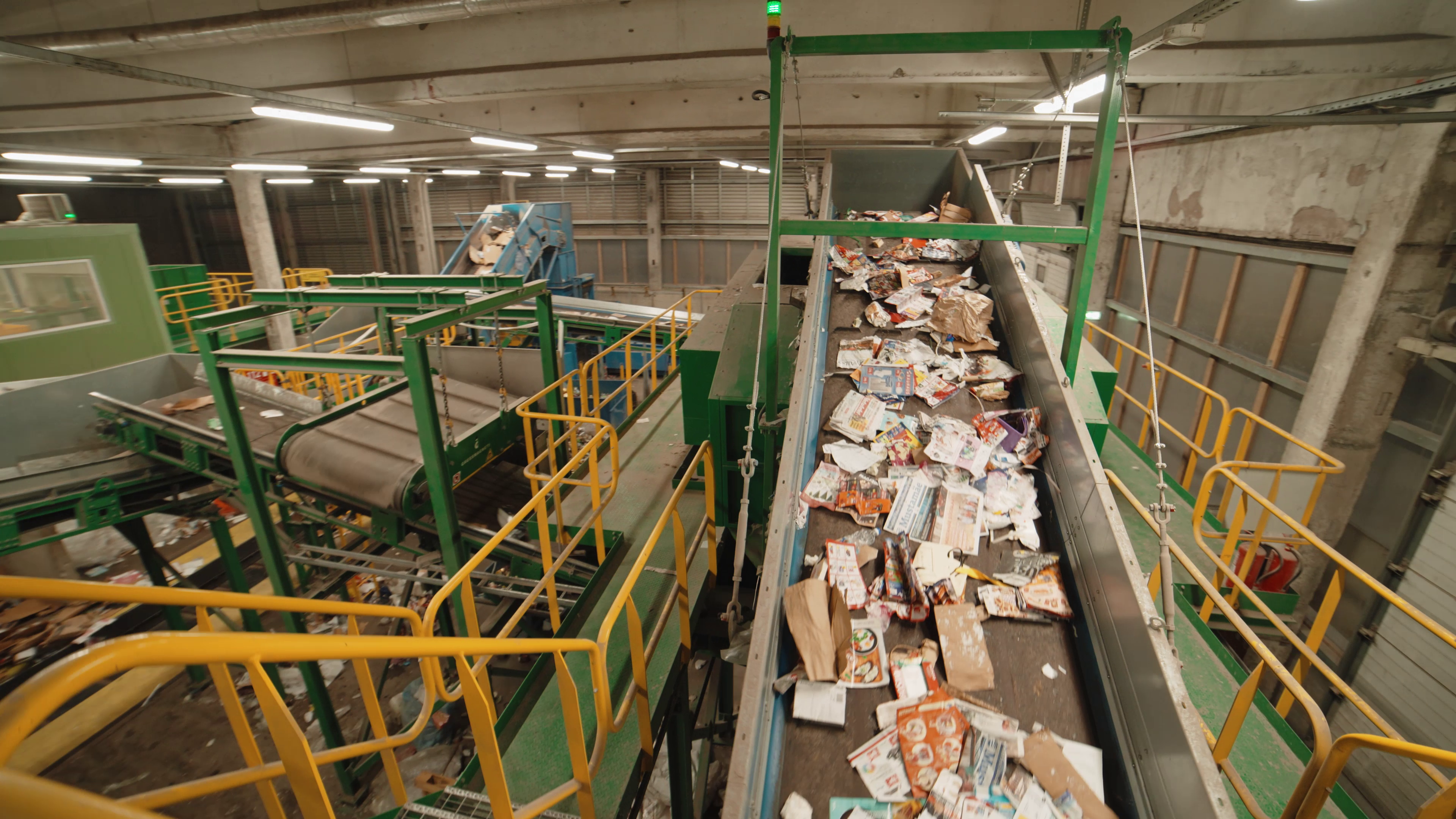
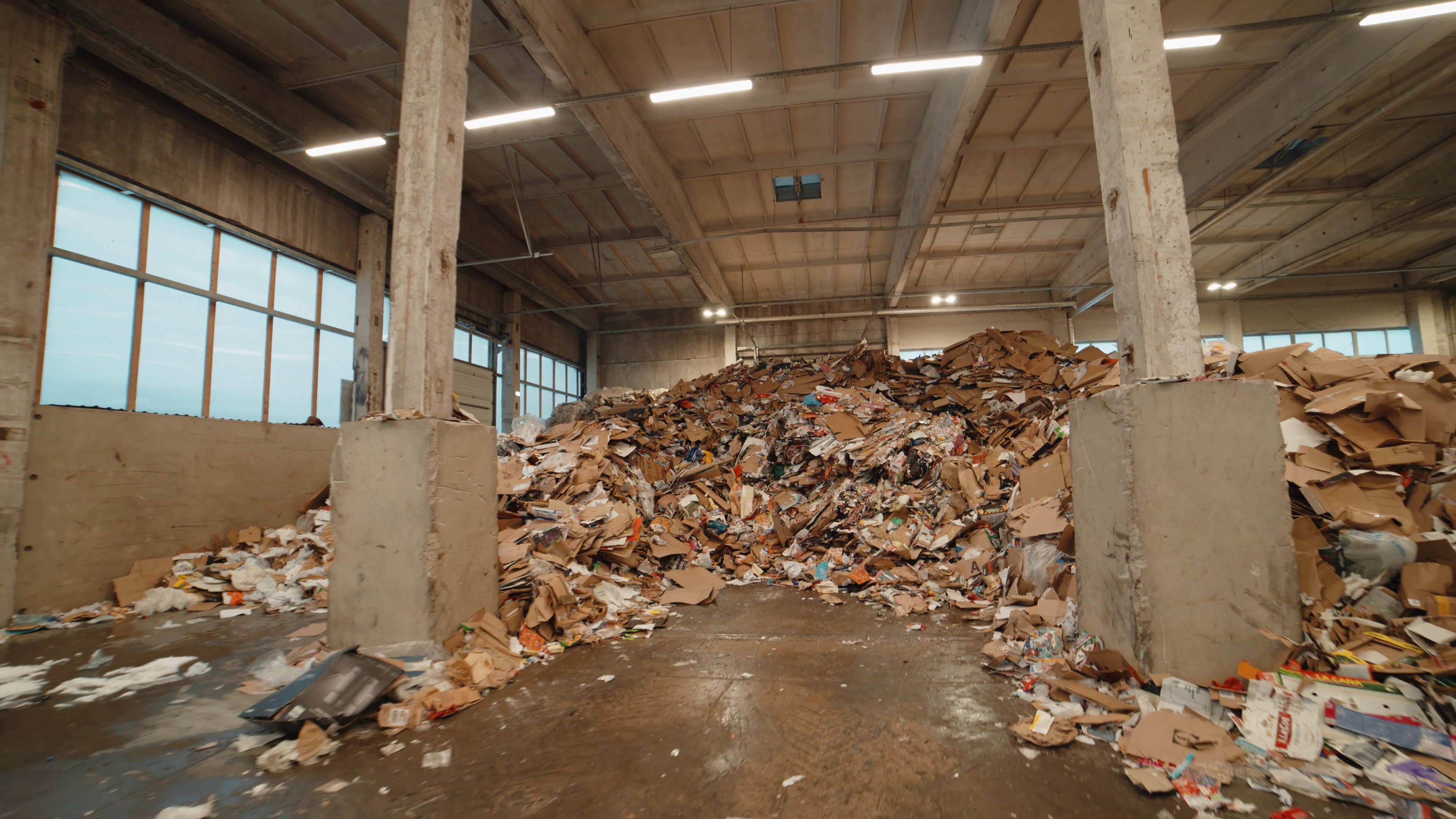
CLOSING NOTES
The partnership between Ragn-Sells and Azortum is an example on how to drive sustainable waste management practices by improving your existing plants and sorting lines.
Sven Ruukholm describes the collaboration:
“Azortum has been also a good partner afterwards. If you, as a customer, forget something or you forgot to ask something, then they point it out and they come back to you to give the best solution. As a customer, they don’t let you make mistakes.”
Don’t just take our word for it. Hear what Ragn-Sells has to say about us!
Write us about your project!
At Azortum, we are committed to developing unique solutions that would be sustainable to operate and profitable for your company.
We have received your information and will be in touch with you shortly. Thanks!